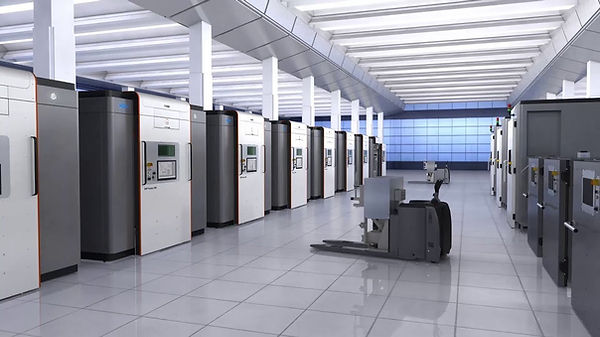
WHAT IS
ADDITIVE MANUFACTURING
Looking to understand Additive Manufacturing?
Let’s explore
​
​
​
​
​
​
​
​
​
​
​
​
​
​
​
​
Additive manufacturing is the official industry standard term used to define the process of joining materials to make objects from 3D model data, usually layer upon layer, as opposed to subtractive manufacturing methodologies.
The primary applications of additive fabrication are design/modeling, fit and function prototyping, and direct part production. Around the world, AM is changing the way organizations design and manufacture products. When used correctly, it can save impressive amounts of time and money. Companies maintain that AM has helped trim weeks, even months, of design, prototyping, and manufacturing time, while avoiding costly errors and enhancing product quality.
​
HOW DOES
3D PRINTING WORK?
HERE’S A SUPER-SIMPLE BREAKDOWN
​
​
​
​
​
​
​
​
​
​
​
​
​
​
It all starts with making a virtual design of the object you want to create. This virtual design is made using CAD software (Computer Aided Design) for the creation of a totally new object or with the use of a 3D scanner to copy an existing object.
Once the 3D model has been created you can start printing. The 3D printing process turns a solid model into thousands of layered slices, then builds each successive layer into a solid object.
Most importantly you need to choose a print technology and material best suited to your application. Read on for printers technologies and materials.
PRINT TECHNOLOGIES
& MATERIALS
NOT ALL PRINT TECHNOLOGIES ARE EQUAL
Not all 3D printers use the same print technology or materials. All are considered additive process’ but differ in the way the layers are built and the material used to create the final object.
Generally speaking there are print technologies that use liquid resins, powders and filaments that are cured, sintered or bound and melted and cooled. Charles (Chuck) Hull created the first 3D printed part on March 9, 1983, through a process he invented called stereolithography. After his first successful print in 1983, Chuck wanted to find a way to commercialize the technology, and it was from this notion that 3D Systems came into being.
In 2010, the American Society for Testing and Materials (ASTM) group “ASTM F42 – Additive Manufacturing”, developed a set of standards that classify the Additive Manufacturing processes into 7 categories according to Standard Terminology for Additive Manufacturing Technologies. For more information you can visit them HERE.
Below are the most common print technologies.
-
SLA – Stereolithography
-
MJP – Multi Jet Printing
-
CJP – Color Jet Printing
-
SLS – Selective Laser Sintering
-
DMP – Direct Metal Printing
-
FDM – Fused Deposition Modeling
SLA
When the process starts, the laser “draws” the first layer of the print into the photosensitive resin. Wherever the laser hits, the liquid solidifies. The laser is directed to the appropriate coordinates by a computer-controlled mirror.
At this point, it’s worth mentioning that most desktop SLA printers work upside-down. That is, the laser is pointed up to the build platform, which starts low and is incrementally raised.
After the first layer, the platform is raised according to the layer thickness (typically about 0.1 mm) and the additional resin is allowed to flow below the already-printed portion. The laser then solidifies the next cross-section, and the process is repeated until the whole part is complete. The resin that is not touched by the laser remains in the vat and can be reused.
MJP
MJP or MultiJet Printing is an inkjet printing process that uses piezo printhead technology to deposit either photocurable plastic resin or casting wax materials layer by layer. MJP is used to build parts, patterns and molds with fine feature detail to address a wide range of applications. These high-resolution printers are economical to own and operate and use a separate, meltable or dissolvable support material to make post-processing a breeze. Another big benefit is that removing support material is virtually a hands-free operation and allows even the most delicate features and complex internal cavities to be thoroughly cleaned without damage.
MJP printers offer the highest Z-direction resolution with layer thicknesses as low as 16 microns. In addition, selectable print modes allow the user to choose the best combination of resolution and print speed, so it’s easy to find a combination that meets your needs. Parts have smooth finish and can achieve accuracies rivaling SLA for many applications. Recent material advances have improved the durability of plastic materials and are now suitable for some end-use applications.
One nice point about MJP printers is that they are office compatible, using standard office electricity to provide convenient and affordable access to high-quality prototypes and indirect manufacturing aids. Office compatibility in concert with their capabilities make MJP printers ideal for direct investment casting applications in jewelry, dental, medical and aerospace applications where digital workflows provide significant time, labor, quality and cost advantages. MJP wax printers also offer a digital drop-in alternative to traditional lost-wax casting processes, eliminating time consuming and costly process steps while utilizing traditional casting methods and materials. All in all, these printers can print virtually any geometry and provide scalable high-volume throughput.
CJP
ColorJet Printing (CJP) is an additive manufacturing technology which involves two major components – core and binder. The Core™ material is spread in thin layers over the build platform with a roller. After each layer is spread, color binder is selectively jetted from inkjet print heads, which causes the core to solidify. The build platform lowers with every subsequent layer which is spread and printed, resulting in a full-color three-dimensional model.
-
Full-color concept models
-
Architectural models
-
Demonstration models
-
Highly complex geometries
-
Quick production times
Whether printed with color or in standard white, parts can be additionally clear coated to add a hard, smooth coating or wax coated to smooth out the surface finish.
SLS
Laser sintering uses a thermal source to fuse powder particles to produce a solid part. The container is initially filled with a powder material whilst a second container remains empty. The two pistons each have a piston positioned, one downwards for the full container and one upwards at the surface for the empty container. Most SLS 3D printers have an accuracy of 100 microns.
With each return, the first piston rises while the second piston is lowered by the thickness of the layer. A roller then passes over the powder and deposits a thin layer on the second container. The deposited layer is then scanned by the laser beam, which merges the powder. This consolidates the shape of the object. The steps are then repeated until the piece is finished.
DMP
Direct Metal Printing (DMP), also commonly known as Direct Metal Laser Sintering (DMLS), is an additive manufacturing technology that builds high quality complex metal parts from 3D CAD data. In the machine, a high precision laser is directed to metal powder particles to selectively build up thin horizontal metal layers one after the other. This cutting edge technology allows for the production of metal parts with challenging geometries, not possible using traditional subtractive or casting technologies. A variety of functional metals are available to print designs, from prototypes to production series of up to 20,000 units.
-
Production of small and extremely complex shapes with no need for tooling
-
High quality parts ideal for R&D and serial part manufacturing at the tightest tolerances
-
Industry’s best surface finished parts with exceptional accuracy
-
Accommodate innovative part design versus conventional processes
-
Topology optimized parts and mass customization
-
Complex and thin-walled structures allow significant part weight reduction
FDM
Fused deposition modelling is a 3D printing process that uses a continuous filament of a thermoplastic material[1]. This is fed from a large coil, through a moving, heated printer extruder head. Molten material is forced out of the print head’s nozzle and is deposited on the growing workpiece. The head is moved, under computer control, to define the printed shape. Usually the head moves in layers, moving in two dimensions to deposit one horizontal plane at a time, before moving slightly upwards to begin a new slice. The speed of the extruder head may also be controlled, to stop and start deposition and form an interrupted plane without stringing or dribbling between sections. Fused filament fabrication was coined by the members of the RepRap project to give a phrase that would be legally unconstrained in its use, given patents covering fused deposition modeling (FDM).
Fused filament printing is now the most popular process (by number of machines) for hobbyist-grade 3D printing.
3D PRINTING
INDUSTRY
INSIGHTS AND DETAILS TO KEEP UP WITH THIS FAST-GROWING INDUSTRY
According to Wohlers Report 2018: “In 2017, the AM industry, consisting of all AM products and services worldwide, grew 21% to $7.336 billion. The growth in 2017 compares to 17.4% growth in 2016 when the industry reached $6.063 billion and 25.9% growth in 2015… The total industry estimate of $7.336 billion excludes internal investments from the likes of Airbus, Adidas, Ford, Toyota, Stryker, and hundreds of other companies, both large and small. A surprising number of the $1-5 billion companies – many of which are unfamiliar to most of us – are investing in AM R&D (research and development).” Source: Wohlers Report 2015
Medical
Rising demand for implants customizations during surgical procedures coupled with growing R&D investments should drive healthcare 3D printing market growth. According to the National Center for Biotechnology Information (NCBI) 2014 data, over next ten years nearly USD 1.9 billion is estimated to be disbursed on medical applications of 3D printing. Such growing investment will boost market growth. Healthcare 3D printing technological advancements and application of advanced devices in the field of bioprinting and tissue engineering should contribute to business growth.
Growing clinical usage of 3D printing in pharmacology such as, poly pill that is used for treatment of numerous diseases should propel healthcare 3D printing market growth. Medical applications of 3D printing are growing significantly including, drug delivery devices and new dosage forms applications. For instance, utilizing medical 3D printing in production of cell cultures, bones, blood vessels, jaw bone, tissues, ears, stem cells, eyeglasses, organs, and vascular networks. Above-mentioned extensive applications will upsurge revenue size.
Source: gminsights
Aerospace & Defense
The aerospace and defense 3-D printing market is estimated to grow at a compound annual growth rate of 23.2 percent over the next five years, reaching $4.76 billion by 2023, according to a MarketsandMarkets report.
This growth is due to the significant reductions in maintenance and production costs of 3-D printed components, as well as high reliability and performance levels of the equipment.
Major players in aerospace and defense have already begun transitioning to additive manufacturing techniques. Many aerospace/Defence contractors have already begun to develop cheaper assemblies using 3-D printing.
Automotive
For the past few decades, 3D printing in the automotive industry was primarily used by carmakers to create automotive part prototypes to check form and fit. Today there are more robust technologies for automotive 3D printing, such as Selective Laser Sintering (SLS) and Direct Metal Printing (DMP), which can be used not only for the production of prototypes but also for end-use parts.
The global automotive industry is expected to reach around US$ 17 billion by the end of 2025.